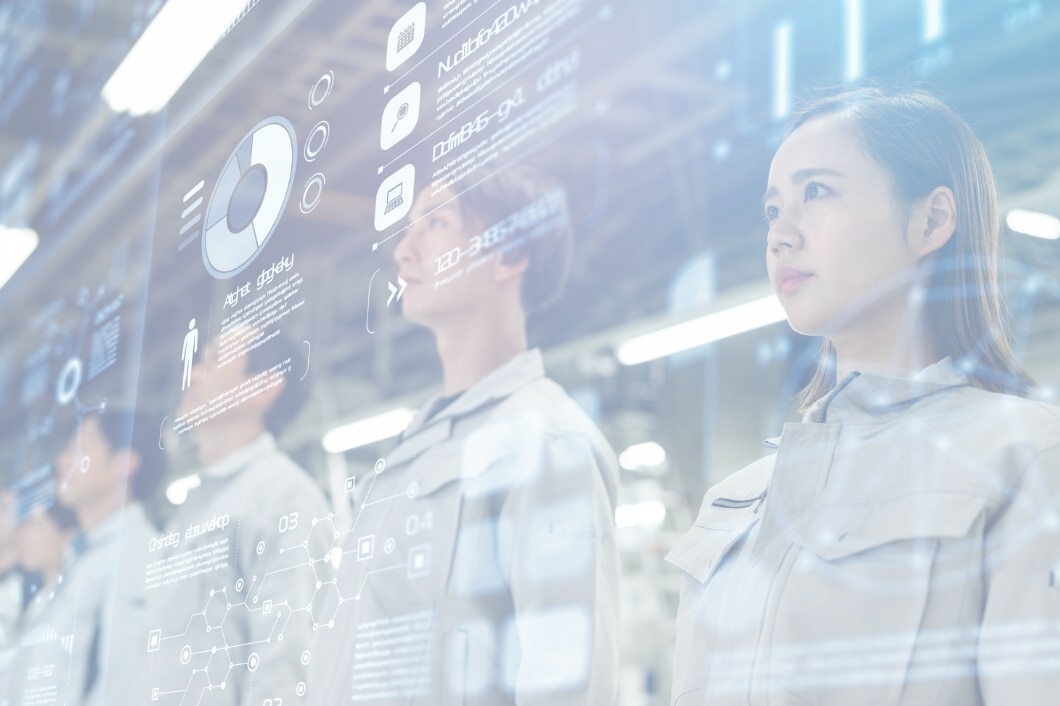
【MRPコラム②】MRP(資材所要量計画)における「基準情報」の考え方とは?(全6回)
MRP(資材所要量計画)有効活用のポイント
前回のコラムでは身近な例(カレーライス)でMRPの基本的な考え方をご紹介しましたが、実際にMRPを導入して有効に活用するためには、以下のポイントがあります。
①基準情報(部品表、手配基準、工程情報など)
②生産計画(販売計画、需要予測、補充計画など)
③在庫管理(下限/上限、コントロールなど)
④実績収集(MRPの土台、リアルタイム、デジタルの活用など)
⑤業務プロセスの変革(限界の解消など)
今回は、MRPにおける基準情報の整備の重要性とポイントについてご紹介します。
目次[非表示]
部品表(BOM:Bill Of Materials)について
MRPで最も重要な基準情報は親子関係を表す「部品表」です。部品表は製品を製造するために必要な部品、原材料の種類と数量を管理しています。プロセス製造業では配合表や、レシピなどと呼ばれていますが、ここでは組立製造業における部品表について説明します。
部品表には、「サマリー部品表」と「ストラクチャー部品表」があります。身近なメガネを例にサマリー部品表とストラクチャー部品表について紹介します。メガネは大きく9つの部品から構成されています。①リム ②ブリッジ ③智(よろい) ④テンプル ⑤クリングス ⑥丁番 ⑦鼻パッド ⑧ダミーレンズ ⑨モダン、メガネAの部品表は、以下のようになります。
メガネAの「サマリー部品表」と「ストラクチャー部品表」
サマリー部品表では、メガネAを作るのに必要な部品と必要数(これを「単位数」といいます)を表記していて想像しやすいと思います。それに対して、ストラクチャー部品表は製造工程や在庫を意識して整理します。具体的に見ていきましょう。
チタンフレームのメガネAは、チタン線材から幾つかの工程(回転冷間鍛造、プレス、バリ取り、切削)を通って、リム、ブリッジ、智、テンプルが作られます。次にリムとブリッジがロウ付けされ、中間品のフロントが作られ、智、テンプル、クリングス、丁番がロウ付けされメガネA中間品が完成します。メガネA中間品を研磨、メッキ・塗装し、鼻パッド、ダミーレンズ、モダンを取り付け、最終調整をしてメガネAが完成します。ここでは大まかな工程を示していますが、実際には200-250工程を通って完成します。
ストラクチャー部品表を整理する上で全ての工程を意識することはできません(意味がありません)。ロウ付けなどの合流工程や、バリ取りや、メッキ・塗装などのバッチ(まとめて処理する)工程、品質管理上の重要な検査工程などの前後には在庫が発生しますので、仕掛在庫を管理する上で、品目を定義します。その結果、ストラクチャー部品表が完成します。次にストラクチャー部品表を管理、運用する上での注意点について考えてみます。
ストラクチャー部品表の管理、運用上の注意点
ストラクチャー部品表を用いると、設計変更時の影響範囲の特定や、品目別の原価計算が容易になります。勿論、所要量計算もしやすく、仕掛品、中間品の在庫管理も可能になります。また、部品表の一元管理にも向いているため、多くの製造業の現場で利用されています。しかし、幾つか注意する点があります。
まず、個別受注生産(受注単位に個別に設計する)の場合は、予め全ての品目や、製造工程が分かりませんし、図面も五月雨式に出力されますので、ストラクチャー部品表による運用が難しい場合があります。
次に、ストラクチャー部品表ができた後でも作業改善などで製造工程が変更される度に部品表を変更する必要があります。また最下層の品目が変更になると、そこから上の階層すべての品目に変更が発生し、階層が深いほどメンテナンスの負担も増加します。
最後に、最も重要なポイントは、自社の生産特性や、前提条件、制約に合わせるのではなく、顧客の要求に合わせた生産プロセスの設計を行うことです。
顧客の要求に合わせた生産プロセス設計
具体的には、顧客の要求するQCD(Quality:品質、Cost:コスト、Delivery:納期)を満足した上で、自社の利益を最大化するストックポイントの設定が重要です。
例えば、個別受注生産では顧客独自の仕様に対応しますのでストックポイントは置かずに設計~出荷までのリードタイムを短縮することを目指します。また、受注組立生産では顧客の要求に合わせて組立を行いますので、必要な部品を在庫しておきます。勿論、製品在庫を持っていても顧客の要求には対応できるかもしれませんが、在庫金額が増え利益を圧迫することになります。
このように顧客の要求を満足し、自社の利益を最大化するには、常に顧客の要求リードタイムを把握し、自社の製造リードタイムを短縮することが必要です。これに合わせて、ストラクチャー部品表を整備します。
改善活動と現場の事実情報のタイムリーな反映
モノづくりの現場では常に改善活動が行われていると思います。しかし、改善結果がタイムリーに基準情報に反映されていることは多くありません。場合によっては生産管理システムを導入したタイミングや、新製品の登録時に基準情報を整備してから更新していない事例も散見されます。
まず、サバを読まないことです。どうしてもリスクを恐れて多めの手配基準や、十分なリードタイムを確保した工程情報などを設定しがちです。欠品や、納期遅れを起こしたくないという責任感からサバを読むことが多くありますが、他部門や、顧客からの信頼を損なうだけでなく、自社の利益に悪影響を与えます。企業が抱えている問題、課題の真因になっていることも少なくありません。
次に、リアルタイムな流れの見える化が必要です。モノの流れや、設備稼働状況、作業者の動線、作業分析など事実情報を見える化した上で事実情報を基にした現場改善を心がけることが重要です。その上で、事実に基づいた基準情報のタイムリーな更新を行いましょう。
MRPを有効に活用するには
今回はMRPにおける基準情報についての考え方や、管理、運用における注意点について紹介しました。MRPを実際に導入して有効に活用するためには、以下のポイントがあります。
①基準情報(部品表、手配基準、工程情報など) ←今回のコラム
②生産計画(販売計画、需要予測、補充計画など)
③在庫管理(下限/上限、コントロールなど)
④実績収集(MRPの土台、リアルタイム、デジタルの活用など)
⑤業務プロセスの変革(限界の解消など)
次回以降のコラムでそれぞれのポイントについてご紹介していきますのでご期待ください。